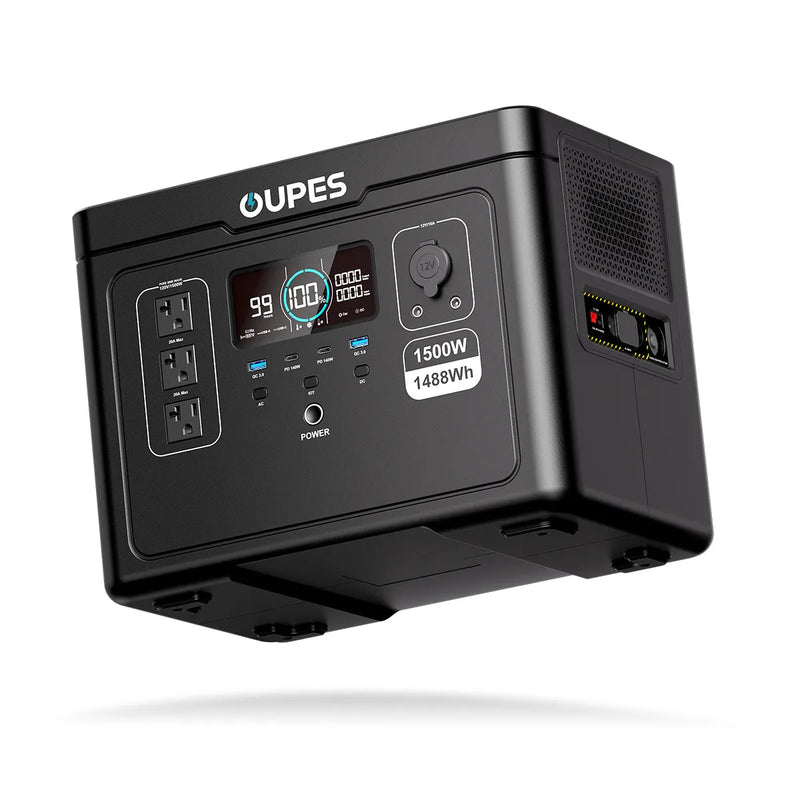
The allure of self-sufficiency often intertwines with a curiosity for creation, leading many to contemplate the construction of their own portable solar power generator. This endeavor resonates with the spirit of innovation—a hands-on approach promising not only potential cost efficiencies but also an intimate understanding of the very technology that grants energy independence. It's a path paved with learning and potential customization. However, embarking on this journey necessitates meticulous planning, a deep respect for electrical principles, and an unwavering commitment to safety. While the satisfaction of assembling a personalized power source is undeniable, it stands in contrast to the integrated engineering, rigorous testing, and comprehensive support embodied in pre-built solutions, such as the thoughtfully designed power stations offered by OUPES, which provide a reliable and immediate pathway to portable power.
To build is to understand. Constructing such a device demands a granular familiarity with its constituent parts and their synergistic interplay. It transforms abstract concepts of energy flow into tangible connections and configurations. This exploration delves into the fundamental components and assembly considerations inherent in crafting a portable solar generator, illuminating the technical landscape while acknowledging the inherent complexities and alternatives available, ensuring that whichever path you choose—bespoke creation or trusted integration—is pursued with clarity and informed purpose.
Blueprinting Your Power: Essential Components Demystified
Architecting a bespoke portable solar generator commences with dissecting the system into its fundamental constituents, each playing an indispensable role in the energy conversion and storage symphony. The primary energy harvester, the **Solar Panel(s)**, forms the crucial threshold where photons embark on their transformation into electrical current via the photovoltaic effect. Selecting the appropriate panel involves navigating choices between monocrystalline (often higher efficiency, potentially higher cost) and polycrystalline types, determining the necessary wattage based on desired charging speed and anticipated solar conditions, and crucially, ensuring the panel's output voltage and current align precisely with the input specifications of the chosen charge controller. Following the flow, the **Charge Controller** acts as the system's intelligent nerve center. Prioritizing a unit employing Maximum Power Point Tracking (MPPT) technology, mirroring the advanced controllers found within OUPES systems, is highly advisable for maximizing energy yield across fluctuating sunlight intensities. This device meticulously regulates the voltage and current directed towards the battery, safeguarding against overcharging while optimizing the energy transfer—a critical function for both efficiency and system longevity. Its specifications *must* harmonize with both the solar array's output and the battery bank's voltage and chemistry. The **Battery Bank** serves as the energy reservoir, the core repository of harvested power. Modern best practice, and the standard embraced by OUPES, heavily favors **Lithium Iron Phosphate (LiFePO4)** chemistry due to its exceptional cycle life (thousands of cycles), inherent thermal stability, and enhanced safety profile compared to alternatives. Calculating the required capacity (Amp-hours or Watt-hours) demands careful assessment of energy needs, while configuring multiple cells requires understanding series (voltage increase) versus parallel (capacity increase) wiring. Absolutely paramount, especially if building a battery bank from individual cells, is the integration of a high-quality **Battery Management System (BMS)** to oversee cell balancing, temperature, and voltage/current limits, preventing damage and ensuring safe operation. Converting the stored DC energy into usable AC power falls to the **Inverter**. Its selection hinges on the required continuous wattage to power your loads and the necessary surge capacity for starting motor-driven appliances. Insistence on a **Pure Sine Wave** inverter is non-negotiable for protecting sensitive electronics, replicating the clean power characteristic of grid electricity and OUPES generators. Finally, the circulatory system—**Wiring, Fuses, and Connectors**—demands meticulous attention. Employing appropriately gauged wires, rated for the anticipated current, minimizes energy loss and prevents overheating. Fuses or circuit breakers, correctly sized and strategically placed, are indispensable safety mechanisms, interrupting dangerous overcurrent conditions. Utilizing high-quality, low-resistance connectors (like MC4 for solar panels or Anderson Powerpoles for high-current DC) ensures secure and efficient electrical pathways throughout the assembly.
The Assembly Nexus: Integrating Components with Precision
Transitioning from discrete components to a functional whole requires a methodical approach steeped in caution and electrical best practices. The assembly process is a nexus where theoretical understanding meets practical application, and where safety must remain the unwavering priority. **Safety First**: It cannot be overstated that working with electrical components, particularly batteries capable of delivering high currents, carries inherent risks. Utilize insulated tools. Wear appropriate personal protective equipment, including safety glasses. Ensure a clear, dry workspace, free from conductive materials. If uncertainty arises regarding any connection or procedure, seeking guidance from experienced individuals or qualified professionals is not just advisable, but essential. A single incorrect connection can lead to component damage, fire, or personal injury. Short, sharp focus on safety protocols is vital. The **Connection Sequence** generally follows a specific logic to protect sensitive components. Typically, the charge controller should be connected to the battery bank *first*. This allows the controller to correctly sense the battery voltage and configure itself before receiving power from the solar panels. Only after the controller-battery link is established should the solar panels be connected to the controller's input terminals. Finally, the inverter and any DC loads should be connected to the battery bank, always through appropriately rated fuses or circuit breakers positioned as close to the battery terminals as practical. Strict adherence to polarity is critical throughout. **Voltage and Polarity Checks** using a multimeter at each stage are mandatory. Reversing polarity (+ to - and - to +) when connecting batteries, panels, or controllers can cause immediate and irreparable damage to the electronics. Double-check. Then check again. Understanding the implications of **Component Configuration**—wiring battery cells or solar panels in series to increase voltage or in parallel to increase capacity/current—is fundamental to achieving the desired overall system voltage and ensuring compatibility between all interconnected parts, as dictated by the specifications meticulously chosen during the blueprinting phase.
Weighing the Path: DIY Diligence vs. Integrated Assurance (OUPES)
The decision to construct a portable solar generator from individual components presents a unique pathway, distinct from acquiring a pre-engineered, integrated solution. The DIY route undeniably offers avenues for deep customization; one can theoretically handpick every component to meet highly specific, perhaps unconventional, requirements. It fosters an unparalleled learning experience, cultivating an intimate understanding of electrical principles and energy systems. Furthermore, if components are sourced astutely and potential pitfalls are navigated successfully, there *may* be opportunities for cost savings compared to purchasing a retail unit of equivalent raw specifications. This possibility beckons the hands-on enthusiast. However, this path is demanding. It necessitates a substantial investment in time—time for research, component sourcing, meticulous assembly, and inevitable troubleshooting. It requires a significant level of technical proficiency in electronics and electrical wiring; errors can be costly, both financially and in terms of safety. Component compatibility presents a constant challenge; ensuring the solar panel voltage, charge controller parameters, battery chemistry and voltage, BMS capabilities, and inverter specifications all harmonize perfectly requires careful diligence. Unlike a unified product, there is no single overarching warranty; guarantees reside with individual component manufacturers, complicating potential claims. Troubleshooting becomes solely the builder's responsibility. Contrast this with the integrated assurance offered by a professionally engineered solution, such as those developed by OUPES. Here, components are not merely assembled but holistically designed and rigorously tested to function in perfect synergy. Sophisticated safety mechanisms and advanced BMS protections are integral, not add-ons. The complexities of component matching are expertly resolved by engineers. The result? A reliable, user-friendly device offering predictable performance, backed by a comprehensive warranty and dedicated customer support. OUPES represents a commitment to accessible, dependable power, where the intricate engineering is handled, delivering peace of mind alongside portable energy.
In conclusion, constructing a personalized portable solar power generator is an ambitious undertaking, a testament to the spirit of self-reliance and technical curiosity. It demands rigorous planning, careful component selection, unwavering attention to safety protocols, and a significant investment of time and expertise. Success yields a custom-tailored power source and invaluable knowledge. However, the path is intricate, fraught with potential challenges related to compatibility, safety, and troubleshooting, requiring a level of diligence not to be underestimated.
While the DIY journey offers its unique rewards, the readily available alternative of integrated, factory-built systems provides a compelling proposition. Solutions from OUPES encapsulate sophisticated engineering, optimized component synergy utilizing robust LiFePO4 technology, and built-in safety features within a user-friendly package. They offer a proven, reliable, and often more practical route to achieving portable power independence, supported by warranties and dedicated service, ensuring that dependable energy is accessible without necessitating the complexities and risks inherent in ground-up construction. The choice hinges on balancing the desire for customization and learning against the pragmatic advantages of integrated assurance and professionally validated performance.